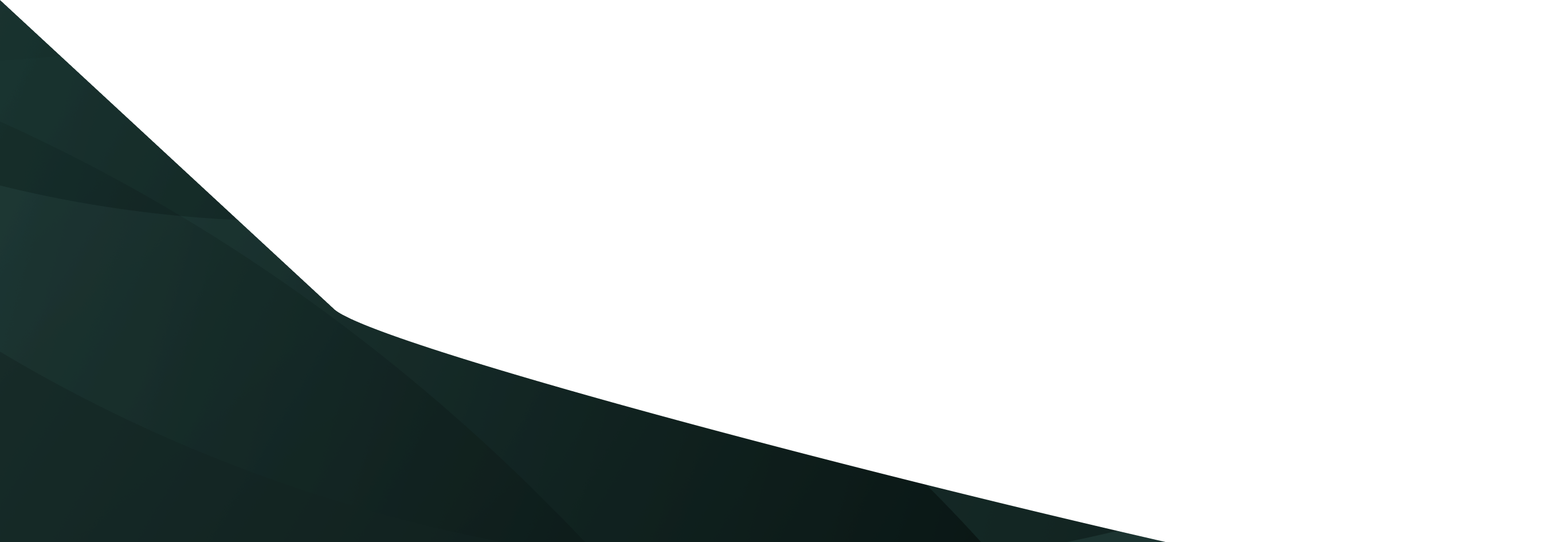

Helping farmers and growers succeed, from the ground up
We provide the highest-quality nutrients, world-class soil science, and practical advice for every kind of farm system in Aotearoa New Zealand.
Like all farmers, we want farming to keep going strong for generations. That’s why we back smarter ways of working that care for the land, boost productivity, and leave things better for those coming next.
Find out what we're all about, how we’re tracking, and how you can join a co-op that’s backed Kiwi farmers for over 45 years.
Meet our leadership team
Meet our board
Latest news
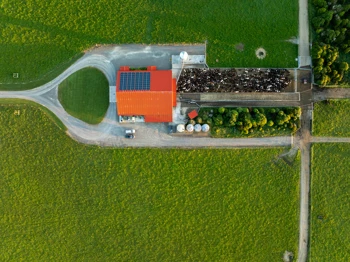
News & advice
01 May 2025
Fonterra invests in EcoPond pilot to reduce on-farm emissions
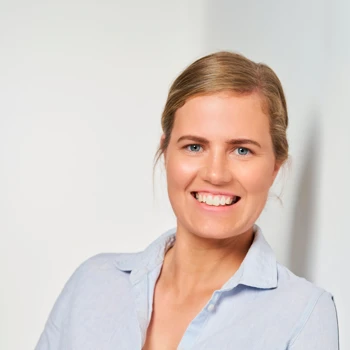
News & advice
01 April 2025
Where Are They Now? – Ravensdown Hugh Williams Memorial Scholarship
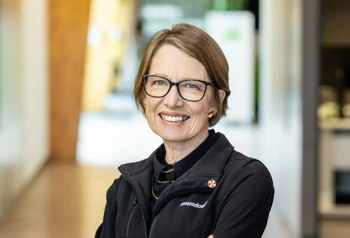
News & advice
05 March 2025
Lifting the lid on governance
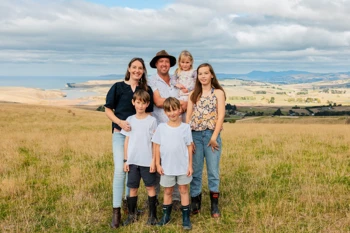
News & advice
23 April 2025
Where Are They Now? – Ravensdown Hugh Williams Memorial Scholarship